In today’s fast-paced business environment, optimizing warehouse operations is vital for companies looking to stay competitive. One technology that has revolutionized the way goods are stored and retrieved is Automated Storage and Retrieval Systems (AS/RS). In this article, we will explore the benefits and capabilities of AS/RS and why they are becoming increasingly essential for businesses across various industries.
Benefits and Capabilities of Automated Storage and Retrieval Systems (AS/RS)
The AS/RS system offers various benefits that enable businesses to optimize their supply chain management, streamline operations, and ultimately deliver a better customer experience.
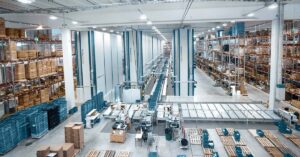
Increased Storage Density
Traditional warehouse storage methods often result in wasted space due to inefficient use of vertical and horizontal areas. AS/RS leverage advanced algorithms and computer-controlled machinery to maximize storage density. By utilizing vertical space and compact storage configurations, businesses can significantly increase their storage capacity without expanding their physical footprint. This not only saves costs but also allows for better space utilization and inventory management.
Improved Inventory Accuracy
Manual inventory management is prone to human error, leading to misplaced or lost items, inaccurate stock counts, and costly discrepancies. AS/RS, on the other hand, offers precise inventory tracking and real-time visibility. With the integration of barcode or RFID technology, these systems ensure accurate inventory counts, reducing the risk of stockouts, overstocking, and fulfillment errors. This level of accuracy enhances overall operational efficiency and customer satisfaction.
Enhanced Order Picking Efficiency
Order fulfillment is a critical process that can significantly impact customer satisfaction and operational costs. AS/RS streamline order picking through automated cranes or robots that retrieve items from storage locations and bring them to human operators. This eliminates the need for manual searching and reduces travel time, resulting in faster and more accurate order fulfillment. Additionally, AS/RS can prioritize orders based on urgency, optimizing the picking sequence and further improving overall efficiency.
Reduced Labor Costs
Labor costs are a significant concern for businesses, especially in labor-intensive warehouse operations. AS/RS minimize the reliance on manual labor by automating the storage and retrieval processes. This reduces the need for extensive human involvement and allows employees to focus on more value-added tasks. With fewer labor requirements, businesses can save costs, increase productivity, and allocate resources to other areas of their operations.
Faster Order Fulfillment
In today’s era of instant gratification, customers expect quick and efficient order fulfillment. AS/RS enables businesses to meet these expectations by significantly reducing order processing times. The integration of AS/RS with warehouse management systems (WMS) optimizes order sequencing and enables real-time inventory updates, ensuring faster order picking and shipping. This speed and accuracy enhance customer satisfaction, improve retention rates, and provide a competitive advantage in the market.
According to Fact.MR’s analysis, the global automated storage and retrieval systems (ASRS) market is expected to reach US$ 24 billion by 2032. Also, North America holds an absolute dollar opportunity of around US$ 4,844 million.
Different Types of Automated Storage and Retrieval Systems
There are several types of Automated Storage and Retrieval Systems (AS/RS), each designed to meet specific storage and retrieval requirements. Here are some common types:
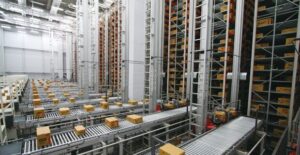
1. Unit Load AS/RS: This type of system is used for handling large, heavy, or palletized loads. It typically consists of cranes or robots equipped with forks or clamps that can lift and transport entire pallets or large containers. Unit Load AS/RS is suitable for high-density storage and retrieval of bulk items.
2. Mini Load AS/RS: Mini Load AS/RS is designed for handling smaller loads, such as totes, cartons, or trays. It utilizes smaller cranes or robots that can access narrow aisles and retrieve individual items from storage locations. This type of system is commonly used in e-commerce, pharmaceuticals, and other industries with high item turnover rates.
3. Vertical Lift Modules (VLM): VLM systems consist of vertically arranged columns with trays or shelves. These modules automatically retrieve requested trays and bring them to an ergonomic access point for operators. VLM systems optimize vertical space utilization and are ideal for storing small to medium-sized items.
4. Vertical Carousel Systems: Vertical carousels are similar to VLMs but consist of rotating shelves or carriers that bring the required items to the operator. This system is well-suited for batch picking and high-speed item retrieval.
5. Horizontal Carousel Systems: Horizontal carousels are circular systems with multiple bins or shelves that rotate horizontally, bringing the requested items to the operator. These systems are commonly used in order-picking applications and offer fast and efficient retrieval of small to medium-sized items.
6. Shuttle Systems: Shuttle systems use robotic shuttles that move horizontally within a racking structure to retrieve items. These shuttles can access multiple levels and aisles, enabling high-density storage and efficient retrieval of items. Shuttle systems are flexible and scalable, making them suitable for various applications.
These are just a few examples of AS/RS types available in the market. Each system has its own advantages and is selected based on factors like item characteristics, storage capacity requirements, throughput speed, and available space. It’s important to assess specific business needs before choosing the most appropriate AS/RS type for a particular application.
Conclusion
Automated Storage and Retrieval Systems have transformed the way businesses manage their warehouse operations. By leveraging advanced technology and automation, AS/RS offers increased storage density, improved inventory accuracy, enhanced order-picking efficiency, reduced labor costs, and faster order fulfillment. These benefits enable businesses to optimize their supply chain management, streamline operations, and ultimately deliver a better customer experience.
As the demands of the modern market continue to evolve, investing in AS/RS is no longer a luxury but a necessity for businesses looking to remain competitive and efficient. By embracing this technology, companies can position themselves for success, improve operational efficiency, and drive sustainable growth in an increasingly dynamic business landscape.
Also Read:
1. Maximizing Safety & Efficiency: Exploring Latest Trends and Developments in Smart Tire Technology
2. Transparent OLED: Illuminating the Future of the Display Industry