Thermal spray coatings have emerged as a versatile solution for enhancing the durability, performance, and lifespan of various industrial components. This article aims to shed light on the business and industry scope of thermal spray coatings, highlighting their unique advantages and potential for growth.
1. Diverse Applications
Thermal spray coatings find applications across industries such as aerospace, automotive, oil and gas, power generation, and manufacturing. These coatings are used to protect against corrosion, wear, erosion, heat, and chemical damage. Whether it’s protecting turbine blades in a power plant or improving the lifespan of automotive engine components, thermal spray coatings offer a reliable solution.
The coatings can be tailored to meet specific requirements, ensuring optimal performance in various environments and under extreme conditions.
2. Enhanced Component Performance
Thermal spray coatings improve the performance and functionality of components by increasing hardness, reducing friction, and enhancing resistance to extreme conditions. By applying a thermal spray coating, components gain improved wear resistance, reduced friction, and increased durability. This leads to extended operational life and reduced downtime for equipment.
For example, in the aerospace industry, thermal spray coatings are used to protect engine components from high temperatures and corrosive environments, enhancing their performance and reliability.
3. Wide Range of Coating Materials
Thermal spray coatings can be applied using various materials, including metals, ceramics, polymers, and composites. This flexibility allows businesses to choose coatings tailored to their specific needs. Different materials offer different properties, such as high temperature resistance, enhanced corrosion protection, or improved electrical conductivity.
For instance, ceramics are commonly used for their high temperature and wear resistance, while metals like stainless steel can provide excellent corrosion protection.
According to a latest report by Fact.MR, the sales of thermal spray coatings were valued at US$ 7.1 Billion in FY 2021, and are forecast to register a Y-o-Y expansion rate of 11.3% in 2022, expected to close at US$ 7.9 Billion.
4. Cost-Effective Solution
Thermal spray coatings offer a cost-effective alternative to replacing worn-out or damaged components. By extending the lifespan of existing equipment, businesses can save on capital expenditures. Instead of investing in new machinery or parts, applying a thermal spray coating can restore functionality and performance at a fraction of the cost.
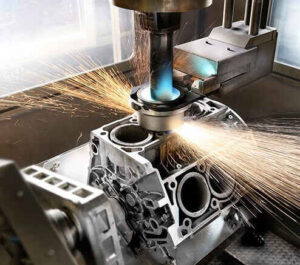
5. Growing Demand
The increasing need for high-performance, durable components in industries such as aerospace and energy is driving the demand for thermal spray coatings. As industries strive for improved efficiency, reduced maintenance, and enhanced equipment lifespan, thermal spray coatings have become an essential solution. The market for thermal spray coatings is projected to witness significant growth in the coming years.
6. Technological Advancements
Ongoing research and development efforts are focused on improving coating materials, application techniques, and equipment. This leads to more efficient and reliable thermal spray coating processes. Advancements in coating materials, such as nanocoatings, are enhancing performance and expanding the range of applications.
Additionally, advancements in equipment technology are improving the precision and quality of thermal spray coatings, ensuring consistent and uniform coatings.
7. Environmental Considerations
Thermal spray coatings are eco-friendly compared to traditional coating methods, as they generate less waste and use fewer harmful chemicals. The process typically involves minimal environmental impact, making it a more sustainable choice for businesses. This aligns with the growing emphasis on sustainable manufacturing practices and environmentally conscious operations.
8. Business Opportunities
The growing demand for thermal spray coatings opens up opportunities for manufacturers, service providers, and suppliers in the coating industry. Companies that offer specialized coating services and advanced equipment can capitalize on this trend. By providing high-quality coatings, tailored solutions, and efficient application processes, businesses can establish themselves as leaders in the thermal spray coating market.
What materials are used in Thermal Spray Coatings?
Thermal spray coatings can be applied using a wide range of materials, each offering unique properties and advantages. The choice of coating material depends on the specific application and desired performance characteristics. Here are some commonly used materials in thermal spray coatings:
1. Metals:
– Aluminum: Offers excellent corrosion resistance and thermal conductivity.
– Stainless Steel: Provides high corrosion resistance and good mechanical properties.
– Nickel and Cobalt Alloys: Known for their high-temperature resistance and wear resistance.
– Titanium: Offers lightweight and high-strength characteristics.
2. Ceramics:
– Oxides (such as Alumina, Zirconia, and Chromia): Provide excellent wear resistance, high-temperature resistance, and electrical insulation properties.
– Carbides (such as Tungsten Carbide and Chromium Carbide): Known for their exceptional hardness and wear resistance.
– Nitrides (such as Titanium Nitride and Aluminum Nitride): Offer high-temperature resistance, hardness, and low friction properties.
3. Polymers:
– Polyesters: Provide excellent chemical resistance and electrical insulation properties.
– Polyurethanes: Known for their excellent wear resistance, flexibility, and impact resistance.
– Polyimides: Offer high-temperature resistance, chemical resistance, and low coefficient of friction.
4. Composites:
– Metal Matrix Composites (MMC): Combine metals with ceramic reinforcements to provide enhanced mechanical properties and wear resistance.
– Ceramic Matrix Composites (CMC): Combine ceramics with ceramic reinforcements to offer high-temperature resistance, improved toughness, and wear resistance.
Benefits of Thermal Spray Coatings
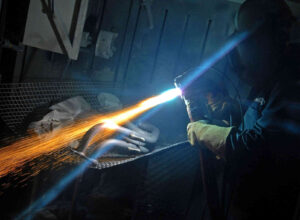
Here is the list of few benefits offered by the Thermal Spray Coatings
1. Enhanced durability and lifespan of components through improved wear and corrosion resistance.
2. Increased performance and functionality of parts by reducing friction and improving surface properties.
3. Cost-effective alternative to replacing worn-out or damaged components, saving on capital expenditures.
4. Versatile application across various industries, including aerospace, automotive, and manufacturing.
5. Tailored coatings to meet specific requirements, ensuring optimal performance in different environments.
6. Protection against extreme conditions like high temperatures, erosion, and chemical damage.
7. Improved efficiency and reduced downtime by extending the operational life of equipment.
8. Eco-friendly solution with minimal environmental impact compared to traditional coating methods.
9. Wide range of coating materials available, including metals, ceramics, polymers, and composites.
10. Compatibility with complex shapes and geometries, allowing for efficient coating application.
11. Enhanced surface hardness, reducing the risk of wear and extending the lifespan of components.
12. Customizable thickness and composition of coatings for precise performance requirements.
Conclusion
Thermal spray coatings offer significant business potential due to their diverse applications, enhanced component performance, and cost-effectiveness. As industries seek solutions to improve the durability and efficiency of their equipment, the demand for thermal spray coatings is expected to rise. By leveraging technological advancements and focusing on sustainability, businesses operating in this sector can position themselves for success in a growing market.
Also Read: